108 Ohm Solution Solder Liquid Flux 12 Percent High Solid Content For Soldering Electronics
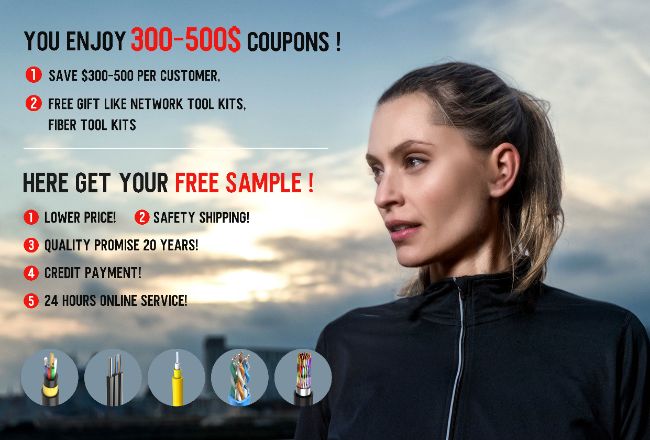
Contact me for free samples and coupons.
Whatsapp:0086 18588475571
Wechat: 0086 18588475571
Skype: sales10@aixton.com
If you have any concern, we provide 24-hour online help.
xAppearance | Light Yellow, Clear And Transparent Liquid | Insulation Resistance | >108Ω |
---|---|---|---|
Solid Content (w/w) | 12.0±0.5 | P H Value | Weak Acid |
Acid Value (mg KOH/g) | 25±5 | Specific Gravity (g/ml) | 0.810±0.008 |
Corrosive | No Corrosive Penetration | Flash Point (T.C.C) | 14℃ |
High Light | 108 ohm solution Solder Liquid Flux,Solder Liquid Flux 12 solid content,liquid flux for soldering electronics ISO9001 |
High activity and high solid content flux special flux for wave soldering of electronic products
1. Introduction
△ TUOPU THC11 flux is a flux with high solid content (12% solid content) and higher activity. It can be used in foaming, spraying and other forms.
△ The resin active system has excellent wettability on the surface of bare copper and solder layer.
△ The welding of multi-layer boards with metallized small holes will show excellent penetration performance.
2. Features and advantages
△ Some special activators added to THC11 flux are used to reduce the surface tension between the solder mask and the solder, which greatly reduces the generation of solder balls.
△ The heat-stable activator in the high-solid no-clean flux reduces the incidence of continuous soldering defects in wave soldering and selective soldering.
3. Technical indicators
Parameter | Typical Value |
Appearance | light yellow, clear and transparent liquid |
Odor | organic solvent |
Insulation resistance | >108Ω |
Solid content (w/w) | 12.0±0.5 |
Flash point (T.C.C) | 14℃ |
Acid value (mg KOH/g) | 25±5 |
Specific gravity (g/ml) | 0.810±0.008 |
Suggested thinner | FD5050 thinner |
Storage time | 12 months |
4. Hazard identification data
Cause of defect | 1 | 2 | 3 | 4 | 5 | 6 | 7 | 8 | 9 | 10 |
Missing | √ | √ | √ | |||||||
Duoxi Webbing | √ | √ | √ | √ | √ | |||||
Tin Cave Viods | √ | |||||||||
Pingoles | √ | √ | ||||||||
Lcicles | √ | √ | √ | √ | √ | √ | √ | |||
Coarse tin Graing | √ | |||||||||
Bridging | √ | √ | √ | √ | ||||||
Balling | √ | √ | √ | √ | √ | |||||
Short circuit Shorts | √ | √ | √ |
Note: √ means possible cause 1. Poor contact between the flux and the bottom plate; improper contact angle of the bottom plate solder 2. The specific gravity of the flux is too high or too low 3. The speed of the conveyor belt is too fast or too slow. Glossy; if it is too slow, it will be slightly round and thick. 4. Too much anti-oxidation oil or deterioration in the tin furnace. 5. The preheating temperature is too high or too low. 6. The temperature of the tin furnace is too high or too low. And short and thick, too low to be thin and sharp and shiny 7. The solder furnace wave crest is unstable 8. The solder in the tin furnace contains impurities 9. The component wiring direction and arrangement are poor. 10. The original board lead is improperly handled.
5.Solder Liquid Flux picture